Electro Soft among first manufacturers in state to participate in new apprenticeship program
June 26, 2017
As anyone involved in U.S. manufacturing will tell you, it’s getting increasingly difficult to find skilled workers. In fact, a Forbes story from earlier this year reported that “the industry is projected to fall a startling 2.0 million workers short” of what it needs to not only replace retiring skilled laborers, but meet demands for growth.
A new program announced June 14 by Gov. Tom Wolf should help address part of that problem, as well as help existing workers receive training in new skills — and Electro Soft is among the first companies selected to take part.
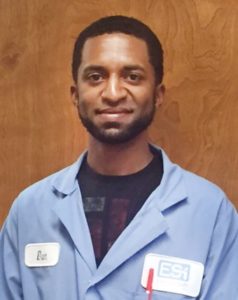
The Department of Labor & Industry’s Apprenticeship and Training Office added five new apprenticeship programs and two new apprenticeship occupations as a way to help employers train the workers they need and assist job seekers to find a career path to better-paying jobs.
“Our first apprentice will be Dan Wallace,” says Electro Soft Executive Vice President Karla Trotman. “He is enrolled at North Montco Technical School taking Mechatronics (technology combining electronics and mechanical engineering) classes for the in-class portion of the apprenticeship.” Wallace, a current employee at Electro Soft, “will be using the program to develop his skill set to rise through the ranks of the company,” she says. “We look at all employees who have an interest across all areas of the business. Our goal is to then bring in new hires to fill the positions that were left by the apprentice, training them in the basics and hopefully moving them up through the organization.”
Trotman worked closely with Stuart Bass, executive director of the Keystone Development Partnership, to “customize the Industrial Manufacturing Technician (IMT) apprenticeship for Electro Soft,” Bass says. She then “connected with North Montgomery County Tech to provide the classroom training.”
Keystone Development defines apprenticeship as “an employer-driven program that combines on-the-job learning with job-related instruction to build worker skills and establish pathways to higher levels of employment and wages.”
The Industrial Manufacturing Technician hybrid apprenticeship program last 18 months (or 3,000 hours) and “trains workers to set up, operate, monitor, and control production equipment; help improve manufacturing processes and schedules to meet customer requirements; understand manufacturing as a business system that integrates multiple disciplines, processes, and stakeholders; efficiently and safely manage raw materials and consumables.”
Related courses include Industrial Math for the Trades & Blueprint Reading; Industrial Manufacturing, CPR, OSHA 10; and 4 Manufacturing Skill Standards Council (MSSC) modules: safety, quality practice & measurement, manufacturing processes & production, and maintenance awareness.
Apprentices must also have on-the-job training that provides demonstrated competency in operating production equipment; interpreting technical information; measuring and inspecting work using mechanical tools and testing equipment; routine equipment maintenance; and much more.
When they’re done with training, apprentices earn nationally recognized manufacturing journey worker credentials.